Flat Thread Rolling Dies: The Key to Stronger, Faster Fastener Production
- accusizecarbidepro
- Mar 26, 2024
- 5 min read
In the world of manufacturing, the quest for efficiency and quality is unending. Nowhere is this more apparent than in the production of fasteners. Fasteners, such as bolts, screws, and studs, are ubiquitous in virtually every industry, holding together the very fabric of modern society. To meet the demands of industries ranging from automotive to aerospace, manufacturers must continuously innovate their production processes. In this pursuit, one technology stands out as a game-changer: flat thread rolling dies. These precision-engineered tools play a crucial role in enhancing the strength, speed, and quality of fastener production. In this comprehensive guide, we will explore the intricacies of flat thread rolling dies, their advantages, applications, and how they contribute to stronger, faster fastener production.
Understanding Flat Thread Rolling:
Before delving into the specifics of flat thread rolling dies, it's essential to grasp the fundamentals of thread rolling itself. Thread rolling is a cold-forming process that involves deforming the material to form threads, rather than removing material through cutting. This method offers several advantages over traditional cutting techniques, including increased thread strength, improved surface finish, and faster production rates.
Flat thread rolling, as the name suggests, utilizes flat dies with thread profiles machined onto their surfaces. These dies are positioned parallel to each other and apply pressure to the workpiece, displacing material to create the desired thread pattern. The cold-working of the material during rolling results in threads with superior mechanical properties, including higher tensile and fatigue strength compared to cut threads.

Advantages of Flat Thread Rolling Dies:
Flat thread rolling dies offer a multitude of benefits that make them indispensable in fastener production:
Enhanced Thread Strength: One of the primary advantages of flat thread rolling dies is the superior strength of the threads they produce. The cold-working process increases the density and grain flow of the material, resulting in threads that are stronger and more resistant to fatigue and corrosion. This is particularly crucial in applications where the integrity of fasteners is paramount, such as automotive, aerospace, and construction.
Improved Surface Finish: Flat thread rolling dies create threads with smooth, uniform surfaces and precise dimensions. Unlike cut threads, which can exhibit roughness and irregularities, rolled threads have excellent surface finish and dimensional accuracy. This not only enhances the appearance of the fasteners but also ensures proper mating and assembly, reducing the risk of thread galling or seizing.
Increased Production Speed: Flat thread rolling dies enable high-speed, continuous production of fasteners with minimal cycle times. Unlike cutting methods, which require multiple passes to form threads, rolling dies can create threads in a single pass, significantly reducing production time. This increased efficiency allows manufacturers to meet tight deadlines and fulfill large orders more quickly.
Cost-Effective Production: While the initial investment in flat thread rolling dies may be higher than that of cutting tools, the long-term cost savings are substantial. The durability and longevity of rolling dies result in lower tooling costs over time, as they require less frequent replacement and maintenance. Additionally, the high production speeds and reduced scrap rates associated with thread rolling contribute to overall cost-effectiveness.
Versatility: Flat thread rolling dies can be easily customized to accommodate various fastener sizes, thread pitches, and profiles. This versatility allows manufacturers to produce a wide range of fasteners tailored to specific applications and industry requirements. Whether it's coarse or fine threads, metric or imperial sizes, flat thread rolling dies can handle diverse production needs with ease.
Click here to check the list of best flat thread rolling dies manufacturer in India
Applications of Flat Thread Rolling Dies:
Flat thread rolling dies find application across a wide range of industries and fastener types:
Automotive: In the automotive industry, flat thread rolling dies are used to produce high-strength bolts, studs, and other fasteners for critical components such as engines, transmissions, and chassis. The superior strength and reliability of rolled threads make them ideal for withstanding the extreme forces and vibrations encountered in automotive applications.
Aerospace: Aerospace manufacturers rely on flat thread rolling dies to produce precision fasteners for aircraft structures, engines, and systems. The high-quality threads produced by rolling dies ensure tight tolerances and reliable performance in the demanding conditions of aerospace environments.
Construction: In the construction industry, flat thread rolling dies are used to manufacture structural bolts, anchor bolts, and other fasteners for building and infrastructure projects. The strength and durability of rolled threads make them well-suited for securing heavy loads and withstanding the rigors of construction sites.
Machinery: Machinery manufacturers utilize flat thread rolling dies to produce fasteners for industrial equipment, agricultural machinery, and power tools. The fast production speeds and consistent thread quality achieved with rolling dies contribute to the efficiency and reliability of machinery in various applications.
Consumer Goods: Even in everyday consumer products such as furniture, appliances, and electronics, flat thread rolling dies play a vital role in fastener production. The smooth, uniform threads produced by rolling dies ensure proper assembly and long-term durability of consumer goods.
Case Study: Implementing Flat Thread Rolling Dies in Fastener Production:
To illustrate the benefits of flat thread rolling dies in fastener production, let's consider a hypothetical case study of a manufacturing company specializing in automotive fasteners.
Challenge: The company is experiencing issues with the strength and consistency of their threaded fasteners, resulting in frequent failures and customer complaints. Additionally, the slow production speeds and high scrap rates associated with their current cutting process are impeding their ability to meet customer demand.
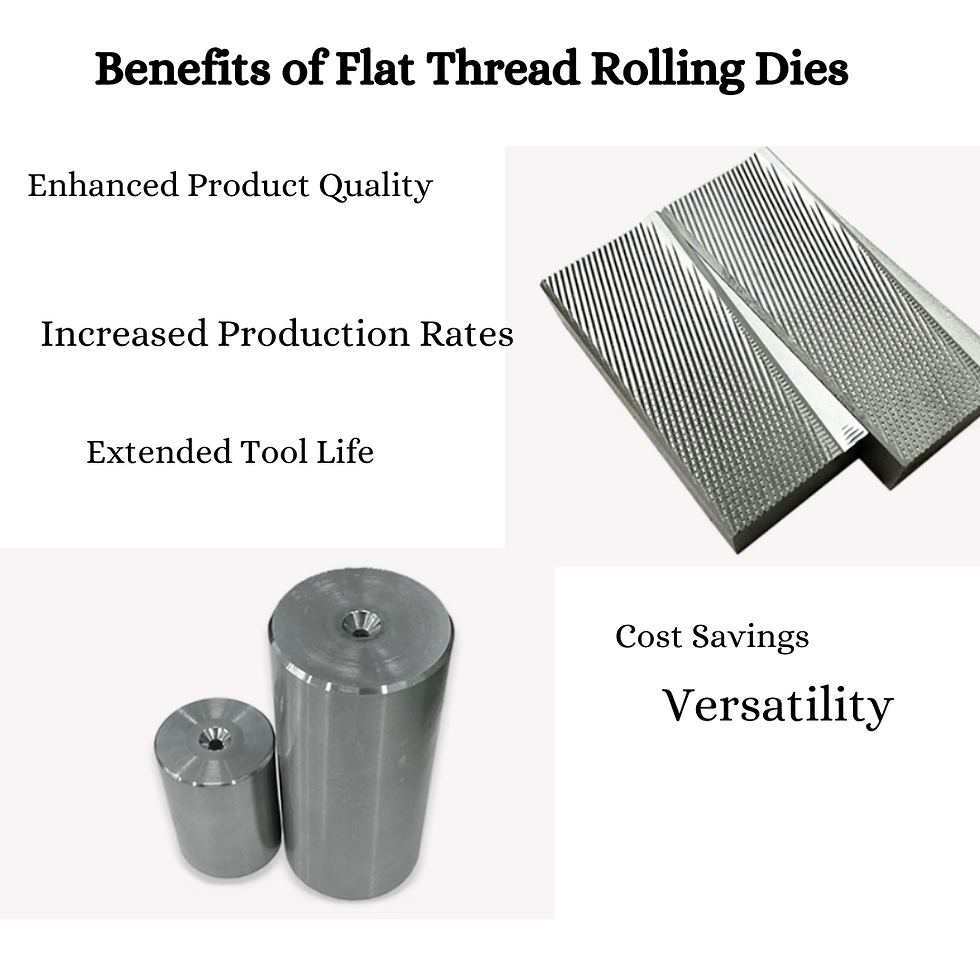
Solution: After conducting a thorough analysis of their production process, the company decides to invest in flat thread rolling dies as a solution to their challenges. They collaborate with a tooling supplier to design and implement custom rolling dies tailored to their specific fastener requirements.
Results: Upon implementing flat thread rolling dies, the company experiences a dramatic improvement in their fastener production:
Thread strength is significantly increased, reducing the incidence of fastener failures and customer complaints.
Production speeds are doubled, thanks to the high-speed, continuous operation of flat thread rolling dies.
Scrap rates are reduced by 50%, resulting in cost savings and improved overall efficiency.
Customer satisfaction improves as the company delivers stronger, higher-quality fasteners with shorter lead times.
Conclusion:
Flat thread rolling dies represent a revolution in fastener production, offering unmatched strength, speed, and quality compared to traditional cutting methods. Whether it's in automotive, aerospace, construction, machinery, or consumer goods, flat thread rolling dies play a vital role in manufacturing the fasteners that hold our world together. By leveraging the benefits of thread rolling, including enhanced thread strength, improved surface finish, increased production speed, cost savings, and versatility, manufacturers can achieve greater success and competitiveness in today's fast-paced market. With flat thread rolling dies as the key to stronger, faster fastener production, the future of manufacturing is brighter than ever.
コメント